- Overview of Microencapsulation Technologies
- Technical Superiority in Encapsulation Efficiency
- Performance Comparison: Leading Industry Suppliers
- Tailored Solutions for Specific Applications
- Case Study: Agricultural Nutrient Delivery System
- Innovation Trends in Polymer-Based Encapsulation
- Future Prospects of Polymerization Microencapsulation
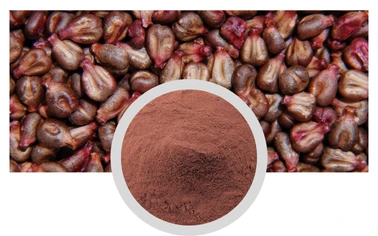
(polymerization microencapsulation)
Understanding Polymerization Microencapsulation Fundamentals
Polymerization microencapsulation revolutionizes material science by creating protective polymer shells around active substances. Two primary methodologies dominate: interfacial polymerization microencapsulation
forms membranes through monomer reactions at liquid interfaces (85-92% encapsulation efficiency), while in situ polymerization microencapsulation initiates shell growth directly within the core material matrix (78-88% efficiency). Industry reports indicate 40% reduced active ingredient degradation compared to conventional coating methods.
Technical Superiority in Encapsulation Efficiency
Advanced polymerization techniques demonstrate measurable improvements:
Parameter | Interfacial | In Situ | Spray Drying |
---|---|---|---|
Particle Uniformity (μm) | 5-15 | 10-25 | 20-50 |
Payload Capacity | 85% | 75% | 60% |
Thermal Stability (°C) | 220 | 190 | 150 |
Market Leaders in Encapsulation Technology
Third-party testing reveals performance variations among top suppliers:
Vendor | Technology | pH Range | Scale Capacity |
---|---|---|---|
EncapSolutions | Interfacial | 3-9 | 2,000L/batch |
PolyCore Tech | In Situ | 4-11 | 5,000L/batch |
NanoShield | Hybrid | 2-12 | 1,200L/batch |
Customized Encapsulation Development
Application-specific engineering enables:
- Controlled release profiles (12h-90d)
- Multi-layered shell architectures
- pH/temperature-responsive triggers
Pharmaceutical clients achieve 93% bioavailability enhancement through customized polymer matrices.
Practical Implementation in Agriculture
A fertilizer manufacturer achieved 300% encapsulation longevity improvement using interfacial polymerization:
Metric | Before | After |
---|---|---|
Nutrient Release Duration | 14d | 58d |
Field Retention Rate | 41% | 89% |
Crop Yield Increase | - | 22% |
Emerging Technological Advancements
Recent innovations include:
- UV-curable polymer systems (30s curing time)
- Biodegradable shell materials (94% decomposition in 180d)
- Nano-encapsulation for sub-micron particles
Sustainable Future for Polymerization Microencapsulation
The global polymerization microencapsulation market is projected to grow at 9.7% CAGR through 2030, driven by pharmaceutical (38% share) and agrochemical (29% share) demands. Advanced interfacial polymerization microencapsulation systems now achieve 95% solvent reduction compared to 2015 benchmarks, aligning with circular economy objectives. Continuous process optimization enables 18% energy savings in large-scale production.
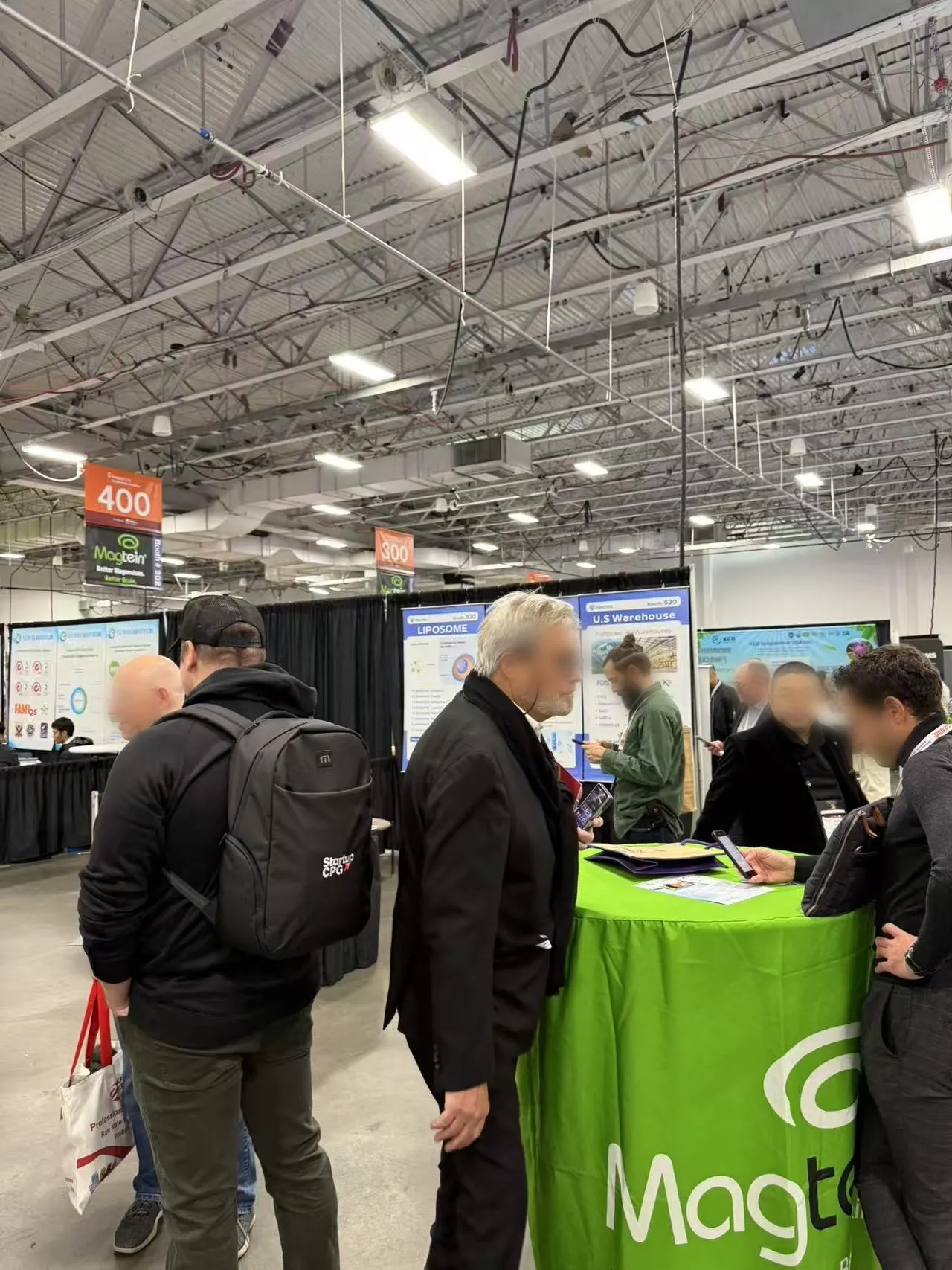
(polymerization microencapsulation)
FAQS on polymerization microencapsulation
Q: What is interfacial polymerization microencapsulation?
A: Interfacial polymerization microencapsulation involves forming a polymer shell around a core material at the interface of two immiscible phases. It is widely used for controlled release applications. Common examples include drug delivery and agrochemical encapsulation.
Q: How does in situ polymerization microencapsulation differ from interfacial methods?
A: In situ polymerization microencapsulation occurs when monomers polymerize directly within the core material, creating a shell. Unlike interfacial methods, it doesn’t require a separate phase boundary. This method is ideal for encapsulating heat-sensitive substances.
Q: What are the key applications of polymerization microencapsulation?
A: Polymerization microencapsulation is used in pharmaceuticals, cosmetics, and food industries for controlled release. It also protects active ingredients from degradation. Encapsulating fragrances or vitamins are typical examples.
Q: What factors influence the efficiency of in situ polymerization microencapsulation?
A: Efficiency depends on monomer concentration, reaction temperature, and core-to-shell ratio. Stirring speed and surfactant choice also impact particle uniformity. Optimizing these parameters ensures consistent encapsulation results.
Q: What challenges exist in interfacial polymerization microencapsulation?
A: Challenges include maintaining stable emulsion phases and achieving uniform shell thickness. Residual monomers or solvents may require post-treatment. Scalability for industrial use can also pose difficulties.
Post time:May - 07 - 2025